2-encoder system
When using encoder 1 and encoder 2, the process values "position", "speed," and "acceleration" are formed from these two encoders in terms of safety.
The function assignment "Process value" should be assigned to the encoder that provides the signal with the better quality for this value.
This is why the selected process value for speed and acceleration is typically assigned to encoder 1, which is the motor encoder, and the selected comparison value is assigned to the second encoder, which is typically an SSI distance encoder.
The selection is typically reversed for the "position" process value because the distance encoder provides better position information.
If both encoders provide values of comparable quality, both encoders can be set to "Process value".
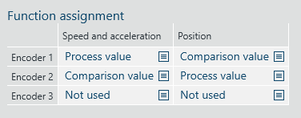

In applications with slip (e.g. storage/retrieval system) or in movements where the applied position is not linear to the motor position (e.g. scissor lift table) and the absolute position is to be monitored, 2 distance encoders can be used in addition to the motor encoder.
This results in the following setting options:
- All 3 encoders are used, but only 2 encoders are considered per process value.
- The motor encoder (encoder 1) and a distance encoder (encoder 2 or encoder 3) are usually used to generate the "speed" and "acceleration" process values. Both distance encoders (encoder 2 and encoder 3) are used to obtain the "position" process value.
INFORMATION
The combination of HTL (encoder 1) and sin/cos (encoder 2) is not permitted.
- To generate the "speed" process values in this constellation, it is possible to calculate speed and acceleration from the two distance encoders (encoder 2 and encoder 3) in addition to the position. In this case, the motor encoder is not necessary. If no SBT brake test is used, an encoder type that is not supported by the safety option can also be used. The SBT brake test uses solely encoder 1 and requires a safe motor encoder.
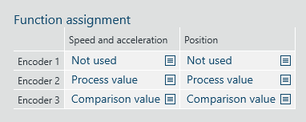
