Encoder evaluation of the CSA31A safety option
The CSA31A safety option supports 1- and 2-encoder concepts that can be parameterized independently for position and speed/acceleration.
In a 1‑encoder concept, the encoder must comply with the necessary safety requirements according to EN ISO 13849‑1 and EN 62061 and be approved for the use of speed/position-dependent safety sub-functions.
The following applies to encoder assignment:
- Encoder 1 is always the motor encoder that is connected to X15 of the device.
- Encoder 2 is the SSI encoder that is used for position control. Alternatively, a sin/cos encoder can also be used.
- Encoder 3 is an SSI encoder that is evaluated exclusively by the CSA31A safety option.
The encoder function is assigned in the Assist CS.. tool in the "Encoder function" dialog. For a 1‑encoder concept, set the function assignment for this encoder to "Process value".
The figure below shows the setting for a safe motor encoder:
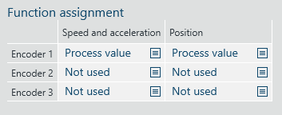

In the case of a 1-encoder concept, the encoder must be referenced again after power on if the safe position is used.
In the case of a 2‑encoder concept, a safe encoder system is formed from 2 encoders. The user is responsible for the selection of components and compliance with the requirements of the relevant standard, e.g. EN ISO 13489. Alternatively, a safe double SSI encoder that meets the required safety requirements according to EN ISO 13849‑1 and EN 62061 and that is approved for the use of speed/position-dependent safety sub-functions can be used.
In this case, encoder 2 and encoder 3 must be configured to "Process value" (see following image):
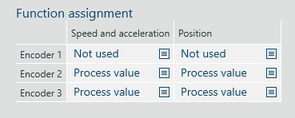

If both encoders are parameterized to "Process value", the system first checks whether both encoder values are within the configured tolerance for position and speed. The mean value is then formed from both encoder values and used in the safety sub-functions for monitoring.
If one of the encoders is parameterized to "Process value" and the 2nd is parameterized to "Comparison value", the difference in both encoder values must be within the tolerance for position and speed. The process value is used for monitoring in the safety sub-functions.
For the response time in the combination of process value and comparison value, take into account the respective tolerance values for position and speed. For averaging, take into account half of the tolerance values in each case.