1-encoder concept – FS motor encoder
The motion variables required by the system are derived from a single motor encoder certified to a recognized FS standard for this purpose.
INFORMATION
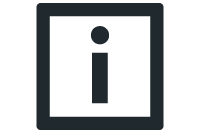
Only safe motor encoders with sin/cos or HTL interface are supported. The safe motor encoder must be connected to the encoder interface X15 of the inverter.
Relative position and speed from FS motor encoder
The safe motor encoder provides an incremental signal from which the speed, direction of rotation, relative position, and acceleration can be derived. The safety sub-functions SS1, SS2, SOS, SLS, SSM, SSR, SDI and SLI are supported. If the EI7C FS is used as a safe motor encoder, the SS1, SLS, SSM, SSR and SDI safety sub-functions are supported.
Absolute position and speed from FS motor encoder
In addition to the relative position described above, MOVISAFE® CSA31A can be used to monitor the absolute position with additional referencing at a known, defined position from the time of referencing. Set the HIPERFACE® encoders to "Only incremental tracks" in the encoder evaluation in the HIPERFACE® evaluation parameter.
INFORMATION
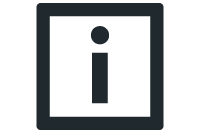
After switching on the voltage supply and in case of an encoder fault, the safety option must be referenced again.
Referencing defines the reference point for the absolute position and is therefore part of the safety chain. The components involved in referencing, such as reference switches, must comply with the safety level (PLr or SIL) required for the safety sub-function (SLP, SCA).