Importing loads into SEW-Workbench
INFORMATION
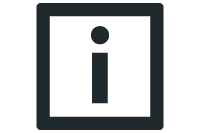
The selection of the gearmotor has an influence on the inertia characteristics of the robot. This is relevant when one motor moves another in the space. In this case, the loads and drives must be simulated and configured sequentially. Start with the drive that is closest to the tool. The new inertias of the gearmotor must then be taken into account in the MOVISUITE® configuration in the inertia properties of the arm section.
Open the SEW-GraphicalWorkbench and proceed as follows:
- You have the "Internal" permission level for the SEW-Workbench
- Add and open a controlled application for each robot drive.
- In the controlled application, select the vertical direction of movement as the movement if the axis can be a vertical drive in one position. Otherwise, select Horizontal/Inclined.
- Select "Vertical – kinematic model" or "Horizontal/Inclined – kinematic model" as the transmission.
- Set the constant data.
- If a MultiAxisController is provided for the axis, adjust the number of drives to the required number.
- Activate, deactivate or parameterize the overhung load calculation specifically for the application. The overhung loads imported later are not taken into account if the overhung load calculation is deactivated.
- Open the kinematic model importer.
- Click […], navigate to the location of the file with the exported load data (for the first controlled application Drive1.txt, for the second Drive2.txt, etc.).
- Click [Open].
- In the kinematic model importer, the corresponding loads are shown for each recorded time step. Selecting [OK] transfers these to the travel diagram.
- Only the self-calculated values of the maximum static torque and the maximum mass moment of inertia of the load from the …_EstimatedMaxApplicationFor_… file have to be entered in the constant data of the travel diagram.
- Set the desired drive data. To do this, select the desired motor and gear unit type.
- The drive search function is started. The search takes correspondingly longer depending on the number of recorded measuring points.
- When the motor is found, jump back to the SEW-Workbench via the results report.
- Repeat the steps in the SEW-Workbench for the remaining drives.
- For the open kinematic chains, the mass of the selected drive must be added to the mass of the corresponding arm section, and the center of gravity and inertia must be recalculated.
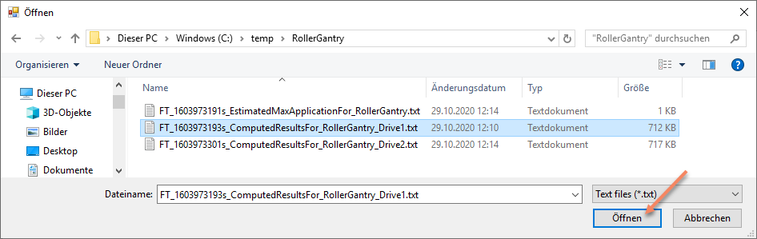
