Systematically measuring friction
Friction must be measured with real drives. Proceed as follows:
INFORMATION
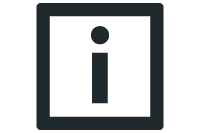
To preserve realistic values for the physics simulation of the drive train, the friction curve should be measured with the robot arm before assembling the drive train.
- Activate the comparison calculation in RobotMonitor. See also chapter Settings.
- Create a trace with the following variable for all axes:
SEW_GVL_Internal.Robot_Axis[i]_PhysicalGearMotor.
fbMotor.fbDeviationCalculator.stOut.
lrCalculatedDeviation_Torque
(Unit: % nominal motor torque in relation to the motor shaft)- Let the drive spin at 100% of the maximum possible speed vmax. The motion can be carried out using an SRL program with two PTP commands in a WHILE loop. For vmax, we recommend using the positive speed application limit in the "Monitoring functions" configuration menu in the "Limit values" submenu of the MOVIKIT® MultiMotion (Parameter 8357.10). The drive must rotate at a constant rotational speed for at least 2-3 seconds after the controller oscillates at the new speed.
- Read the mean value of the Mr,100% friction torque during consistent travel from the trace.
- Let the drive spin at 10% of the maximum possible speed vmax.
- Read the mean value of the Mr,10% friction torque during consistent travel from the trace.
- Calculate the following parameters from the read values:
- Factor of speed-dependent friction: fv = (Mr,100% - Mr,10%)/(0.9 × vmax )
- Constant friction: oc = Mr,10% - fv × 0.1 × vmax
- Smoothing factor of friction curve for direction of rotation reversal: vt = 1% × vmax
- Configure the calculated parameters in MOVISUITE®.
INFORMATION: To determine even more accurate values for configuration, you can add additional measuring points and add an equalizing line in the torque speed diagram. The Y-axis section is oc. The gradient of the straight sections of factor fv.