Linear axis to rotary joint
With this type of crank, the motion of a linear single axis is transferred to the motion of a rotary joint axis.
The crank is configured via the index of the axis and 4 parameters.
Parameterization
Parameter | Description |
---|---|
Joint axis | Index of single axis and joint axis between which the crank operates (for the 1st axis, the value 1 must be entered). |
Parameter 1 | Offset from the rotary joint axis along the robot arm segment that is turned around the rotary joint axis to the pivot joint between the linear single axis and robot arm segment (parameter 1 <> 0) |
Parameter 2 | Additional offset vertically to the robot arm segment, and at the level of movement of the robot arm segment, to the pivot joint between the linear single axis and robot arm |
Parameter 3 | Offset starting from the rotary joint axis along the axis of the robot arm segment at joint axis value 0° to the pivot joint between the base and linear single axis. (Parameter 3 < 0) |
Parameter 4 | Additional offset vertically to the axis of parameter 3, and at the level of movement of the robot arm, to the pivot joint between the base and linear single axis |
Parameters 5..8 | Not used |
Depending on the sign of parameter 1 and parameter 2 or 4, the following 4 cases are distinguished with regard to the position of the linear single axis and robot arm segment.
If parameter 1 is positive, the hinge joint between the linear single axis and robot arm segment is placed along the kinematic chain in the direction of the robot flange as viewed from the rotary joint axis. If, on the other hand, parameter 1 is negative, the hinge joint is placed on an extension of the robot arm segment in the direction of the robot base as viewed from the rotary joint axis.
The resulting crank can be moved within a maximum angle area of 180°, in which case the limit values are not to be approached. The range is obtained by moving the linear single axis between the minimum and maximum possible positions, i.e. the length of the single axis. A change beyond the compression or extension of the crank to the opposite range is not supported. During assembly and startup, make sure that the robot is in the position supported by the configured parameters.
The linear single axis must be referenced during startup by means of a reference offset in such a way that its position corresponds to the length between the two hinge joints.
Parameter 1 > 0 and parameter 2 ≥ 0
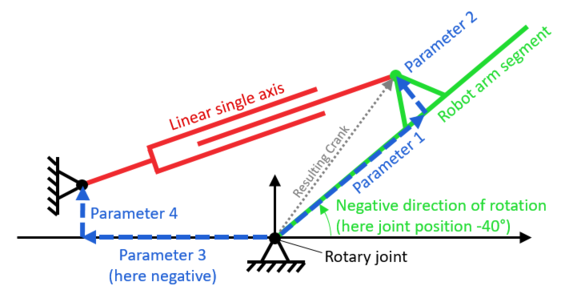

In this case, parameters 1 and 2 are positive, parameter 3 is negative. As parameter 2 is positive, the linear single axis in the figure moves above the rotary joint axis. This behavior is independent of the sign of parameter 4, which is positive in the example shown.
In the example, the robot arm segment has the joint axis value -40 °. If the robot arm segment points in the direction of the first coordinate axis, i.e. horizontally to the right in the figure, it has the joint axis value 0°. For example, if the robot arm segment is pointing vertically upwards, it has the joint axis value -90 °. For example, if it is pointing vertically downwards, it has the joint axis value 90 °. The linear single axis would therefore have to be lengthened to approach 0 °, for example, compared to the position in the figure, and shortened to approach -90 °, for example.
Parameter 1 > 0 and parameter 2 < 0
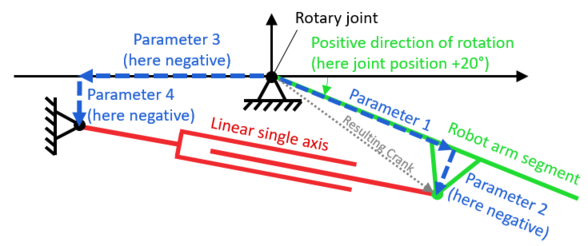

In this case, parameter 1 is positive, parameters 2 and 3 are negative. As parameter 2 is negative, the linear single axis in the figure moves below the rotary joint axis. This behavior is independent of the sign of parameter 4, which is negative in the example shown.
Parameter 1 < 0 and parameter 4 ≥ 0
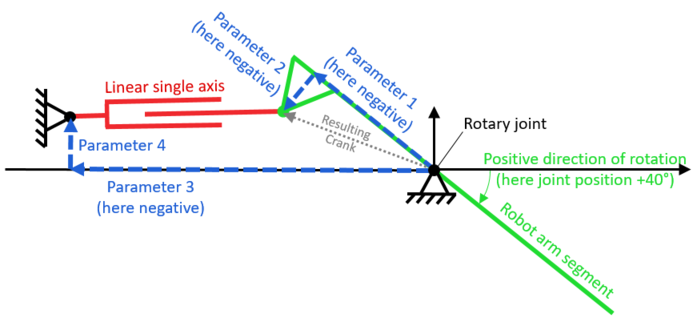

In this case, parameters 1 and 3 are negative, parameter 4 is positive. As parameter 4 is positive, the linear single axis in the figure moves above the rotary joint axis. This behavior is independent of the sign of parameter 2, which is negative in the example shown.
Parameter 1 < 0 and parameter 4 < 0
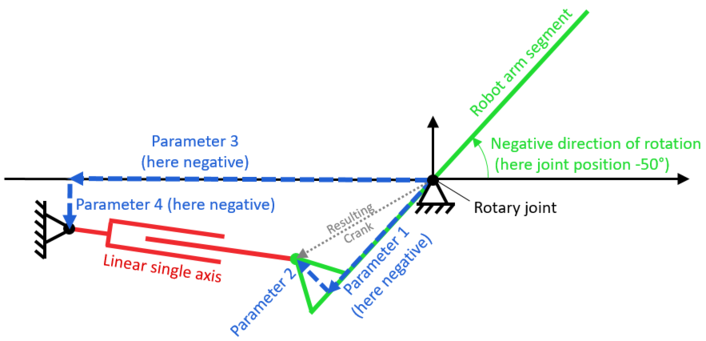

In this case, parameters 1, 3 and 4 are negative. As parameter 4 is negative, the linear single axis in the figure moves below the rotary joint axis. This behavior is independent of the sign of parameter 2, which is positive in the example shown.