Operation without startup
Motor
In its delivery state, the inverter is set to operate a motor according to the specification "Motor power ASM PMot" (corresponds to the specification P(ASM) on the nameplate of the inverter).
Signal terminals
If MOVITRAC® basic is delivered in the delivery state, the following terminal functions are preassigned:
Digital inputs/outputs | |
---|---|
DI01 | Digital input 1, fixed setpoint – positive direction of rotationFactory setting |
DI02 | Digital input 2, fixed setpoint – negative direction of rotationFactory setting |
DI03 | Digital input 3, fixed speed setpoint bit 0Factory setting |
DI04 | Digital input 4, fixed speed setpoint bit 1Factory setting |
DIO01 | Digital input/output, no function, voltage inputFactory setting |
DIO02 | Digital input/output, no function, voltage inputFactory setting |
Analog input | |
---|---|
AI1 | Analog input voltage or current Speed setpoint source: 0 to 10 V; 0 to 1500 min-1 |
Fieldbus
This function is currently still in preparation.
INFORMATION
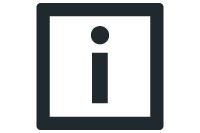
If the inverter is connected to voltage before the mechanical and electrical fieldbus installation, the automatic startup mechanism described below no longer applies.
In this case, the fieldbus gateway, the fieldbus coupling modules, and the MOVIKIT® Velocity Drive software module must be manually configured via the MOVISUITE® engineering software.
The fieldbus interface of the inverter can be used without manual startup (via a keypad or the MOVISUITE® engineering software).
A prerequisite for this is that the following sequence of preparatory measures is followed before the devices are supplied with voltage for the first time:
- Mechanical installation of the CFX11A.. fieldbus gateways and the CFC11A fieldbus coupling modules on the MOVITRAC® basic inverter.
- Electrical installation of the inverter as well as the installed CFX11A.. fieldbus gateways and CFC11A fieldbus coupling modules.
- Switching on the DC 24 V supply of the CFX11A.. fieldbus gateway for the first time via terminals X5:24V/X5:GND
- The connected fieldbus coupling modules and the inverters are supplied with DC 24 V via the fieldbus gateway.
- The fieldbus gateway, the inverters, and the fieldbus coupling modules configure themselves autonomously.
- The inverters automatically load the MOVIKIT® Velocity Drive software module.
- Any connected inverter can now be controlled via fieldbus via the process data assignment of the MOVIKIT® Velocity Drive software module (see documentation "MOVIKIT® Positioning/Velocity Drive").
- Perform a hardware configuration of the fieldbus master.