Starting up the speed controller
Startup is performed without the speed controller first (→ Section "Startup procedure, steps 1 through 17").
1. | The selected operating mode is displayed. If the setting is correct, go to the next menu item. | C00*STARTUP PARAMETER SET 2 VFC n-control
| |
2. | Select the correct encoder type. | C15*ENCODER TYPE INCREM. ENCOD. TTL SINE ENCODER RESERVED | |
3. | Set the correct encoder resolution. | C16*ENC. RESOLUT. 512 inc 1024 inc 2048 inc | |
FOR MOTORS FROM SEW-EURODRIVE | |||
4. | Enter whether the motor has a brake. | C17*BRAKE
WITHOUT WITH | |
5. | Set the stiffness of the closed-loop control system. If the drive tends to oscillate → setting < 1 Transient recovery time is too long → Setting > 1 Recommended setting range: 0.90 – 1 – 1.10 | C18* STIFFNESS 1.000
| |
6. | Enter whether the motor has a flywheel fan (Z fan). | C19*Z FAN
WITHOUT WITH | |
For THIRD-PARTY MOTORS | |||
4. | Enter the moment of inertia of the motor. | D00* J0 OF THE MOTOR 4.600
| |
5. | Set the stiffness of the closed-loop control system. If the drive tends to oscillate → setting < 1 Transient recovery time is too long → Setting > 1 Recommended setting range: 0.90 – 1 – 1.10 | C18* STIFFNESS 1.000
| |
6. | Enter the moment of inertia of the brake and fan. | D00* J BRAKE+FAN 1.000
| |
7. | Enter the mass moment of inertia of the load (gear unit + driven machine) extrapolated for the motor shaft. | C20* 10e–4kgm2 LOAD MOMENT OF INERTIA 0.200
| |
8. | Enter the time for the shortest ramp you want. | C21* s SHORTEST RAMP 0.100
| |
9. | Start the calculation for the startup data by choosing "YES". The process lasts a few seconds. | C06*CALCULATION
NO YES | |
10. | The calculation is performed. After calculation, the next menu item appears automatically. | C06*SAVE
NO YES | |
11. | Set "SAVE" to "YES". The data (motor parameters) are copied to the non-volatile memory of MOVIDRIVE®. | STARTUP DATA IS BEING COPIED...
| |
12. | The startup procedure is now complete. Use the | MANUAL MODE STARTUP COPY TO DBG COPY TO MDX | |
13. | Press the | SIGNATURE QUIT
BASIC VIEW | |
14. | Confirm your selection using the | 0.00rpm 0.000Amp CONTROLLER INHIBIT |
- Once startup is complete, copy the parameter set from MOVIDRIVE® to the DBG60B keypad. You have the following options:
- In the context menu, select the menu item "COPY TO DBG". Confirm your selection using the
key. The parameter set is copied from MOVIDRIVE® to the DBG60B.
- In the context menu, select the menu item "PARAMETER MODE". Select parameter P807 "MDX → DBG". The parameter set is copied from MOVIDRIVE® to the DBG60B.
- The parameter set can now be copied to other MOVIDRIVE® devices using the DBG60B. Plug the DBG60B keypad into the other inverter. You have the following options to copy the parameter set from DBG60B to another inverter:
- In the context menu of the new inverter, choose the "COPY TO MDX" menu item and confirm your entry using the
key. The parameter set is copied from DBG60B to MOVIDRIVE®.
- In the context menu, select the menu item "PARAMETER MODE". Select parameter P806 "DBG → MDX". The parameter set is copied from DBG60B to MOVIDRIVE®.
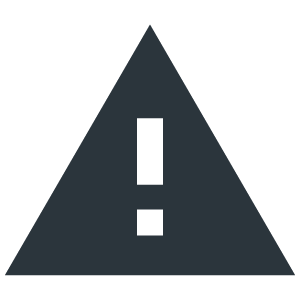
WARNING
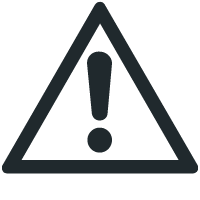
Parameter settings incorrect due to unsuitable data sets.
Severe or fatal injuries.
- In the case of third-party motors, set the correct brake application time (P732 / P735).
- Observe the notes for starting the motor in the section "Starting the Motor" (→ page 102).
- Activate encoder monitoring for TTL and sin/cos encoders (P504 = "ON"). Encoder monitoring is not a safety function.