Actual value description of PI data
The parameters Actual value description PI1 - PI3 define the content of the process input data words transmitted by the frequency inverter to the higher-level controller (see figure below). Each process data word is defined with an individual parameter. Therefore, three parameters are necessary for describing the process input data.
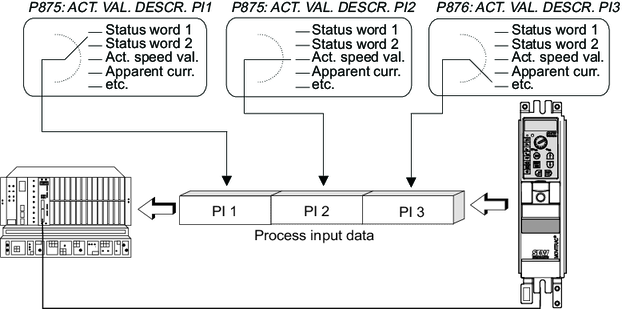

The following parameters can be transmitted across the process data channel using process input data words PI1 to PI3. 32-bit values, such as the actual position, are transmitted in two process data words. You can decide yourself in which process data word the more significant part (high) and the less significant part (low) is transmitted.
Assignment | Meaning | Scaling |
---|---|---|
NO FUNCTION | Assigning a process input data word with NO FUNCTION means that the inverter system does not update this process input data word. In this case, MOVITRAC® B returns the value 0000hex to the higher-level controller. |
|
SPEED | Set to SPEED, the frequency inverter returns the current actual speed in rpm to the higher-level automation system. The actual speed value can only be sent back properly if the inverter can determine the actual motor speed via speed feedback. For applications with slip compensation, the deviation from the real motor speed solely depends on the accuracy of the slip compensation set by the user. | 1 digit = 0.2 / min |
OUTPUT CURRENT | Set to OUTPUT CURRENT, the frequency inverter returns the current actual value of the output current in [% In] to the higher-level automation system (in percent, with reference to the nominal current of the inverter). | 1 digit = 0.1% IN |
ACTIVE CURRENT | By assigning a process input word ACTIVE CURRENT, the frequency inverter provides the actual active current value % In to the higher-level automation system. | 1 digit = 0.1 % IN |
STATUS WORD 1 / STATUS WORD 2 | Assigning status word 1 or status word 2 to the process input data allows for accessing status information as well as fault and reference messages. |
|
SPEED [%] | Set to SPEED [%], the frequency inverter returns the current actual speed in % nmax / P302 to the higher-level automation system. | 4000hex = 100% nmax |
IPOS PI-DATA | Set to IPOS PI (IPOS Process Input Data), an individual actual value can be transmitted from the IPOSplus® program to the higher-level controller via process input data. This setting allows for exchanging up to 48 individually coded bits between the IPOSplus® program and the higher-level controller using the process data channel. You can directly write process input data in IPOSplus® using the command SetSys PI data. For more detailed information, refer to the "IPOSplus® positioning and sequence control system" manual. | Three words with individually coded 16 bits each can be exchanged between the higher-level controller and IPOSplus®. |