Setpoint description of PO data
The parameters setpoint description POx define the content of those process output data words that the higher-level programmable controller sends via the fieldbus system (see following figure).
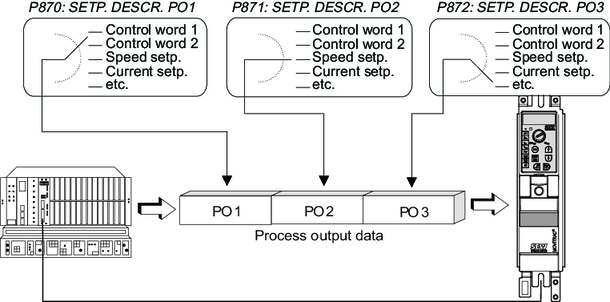

You can use the process output data words PO1, PO2 and PO3 to transmit the mentioned setpoints across the process output data channel. You can decide yourself in which process data word the more significant part (high) or the less significant part (low) is transmitted.
Assignment | Meaning | Scaling |
---|---|---|
NO FUNCTION | The setting NO FUNCTION has the effect that the frequency inverter does not use this process output data word for processing setpoints. The content of the process output data word programmed to NO FUNCTION is ignored although the controller might specifiy a real setpoint via the fieldbus system. The NO FUNCTION setting just disables the processing of the process output data word in the inverter system. However, you can access the process output data at any time using IPOSplus®. |
|
SPEED | Set to SPEED, the MOVITRAC® B frequency inverter interprets the setpoint value transmitted by this process data word to be the speed setpoint if the selected operating mode (P700 operating mode 1, P701 operating mode 2) allows a speed setpoint. If there is no speed setpoint programmed although a communication interface (FIELDBUS, RS485, system bus) has been set as setpoint source, the frequency inverter will use speed setpoint = 0. | 1 digit = 0.2 / min |
CURRENT | Set to CURRENT, the frequency inverter will interpret the setpoint specified in this process data word as current setpoint if a variant with torque control is set as operating mode (P700 Operating mode 1). Else, the frequency inverter ignores the current setpoint. | 1 digit = 0.1 % IN |
MAX. SPEED | Set to MAX. SPEED, the MOVITRAC® B frequency inverter interprets the transmitted setpoint as speed limit. The speed limit is specified in rpm and is interpreted as value for both directions of rotation. The supported value range of the speed limit via fieldbus corresponds to the value range of parameter P302 Maximum speed 1. Specifying the speed limit via fieldbus automatically disables parameters P302 Maximum speed 1, P312 maximum speed 2. | 1 digit = 0.2 / min |
MAX. CURRENT | Set to MAX. CURRENT, the MOVITRAC® B frequency inverter interprets the transmitted process output data as current limit. The current limit is specified in percent with reference to the nominal inverter current in the unit % IN. It is interpreted as value for both directions of rotation. The supported value range of the current limit via fieldbus corresponds to the value range of parameter P303 Current limit 1. The current limits that can be set using parameters P303 Current limit 1 and P313 Current limit 2 are still valid when the current limit is specific using process data. This means these parameters are to be regarded as maximum effective current limit. | 1 digit = 0.1 % IN |
SLIP | Set to SLIP means the MOVITRAC® B frequency inverter interprets the transmitted process output data word as slip compensation value. Specifying the slip compensation via fieldbus automatically disables parameters P324 Slip compensation 1 and P334 Slip compensation 2. Specifying the slip compensation via process data channel is only technically meaningful in the VFC N-CONTROL operating mode because the torque can be influenced directly by changing the slip compensation. The value range of this slip compensation value is identical with the value range of parameter P324 Slip compensation 1 and corresponds to a speed range of 0 - 500 rpm. If the slip specified using process data is outside this value range, the maximum will take effect when the minimum and maximum values are exceeded. | 1 digit = 0.2 / min |
RAMP | Set to RAMP, the MOVITRAC® B frequency inverter interprets the transmitted setpoint value as an acceleration or deceleration ramp. The specified value corresponds to a time in ms and refers to a speed change of 3000 rpm. The rapid stop and emergency stop function is not affected by this process ramp. When transmitting the process ramp via fieldbus system, ramps t11, t12, t21 and t22 become ineffective. | 1 digit = 1 ms |
CONTROL WORD 1 / CONTROL WORD 2 | The assignment of process output data with control word 1 or 2 allows for activating nearly all the drive functions via fieldbus system. For a description of control words 1 and 2, please refer to the chapter "Control word definition". |
|
SPEED [%] | Set to SPEED [%] means the MOVITRAC® B frequency inverter interprets the setpoint transmitted in this process data word as speed setpoint in percent. The relative speed setpoint always refers to the currently applicable maximum speed limit, which means either P302/312 or MAX. SPEED or PO speed limit. | 4000hex = 100% nmax |
IPOS PO-DATA | The setting IPOS PO-DATA has the effect that the frequency inverter does not use this process output data word for processing setpoints. The inverter system ignores the content of the process output data word programmed to IPOS-PO-DATA and is available for sole processing in the IPOSplus® control program. Within IPOSplus®, you can use the command GetSys PO-Data to directly access the process output data of the communication interfaces. For more detailed information, refer to the IPOSplus® positioning and sequence control system manual. | Three words with individually coded 16 bits each can be exchanged between the higher-level controller and IPOSplus®. |