Introduction
The acknowledgment of a warning, the start inhibit, a fault and a limit violation can be realized via a safe digital input F‑DI or via the "Fault acknowledgment" bit of the safe process data.
To acknowledge a fault or a limit value violation via a safe digital input, an input must be set to "Acknowledge faults" or "Unlatch latched F-DI and acknowledge faults".
Acknowledgment is performed by a 0 → 1 edge. In the following cases, a warning will be indicated after 20 s:
- A permanent high signal is present on the safe digital input to which the acknowledgment has been assigned.
- One of the fault acknowledgment bits in the process data is permanently "1".
To acknowledge faults via PROFIsafe or CIP Safety™, the exchange of safe data of the safety option must be fault-free. Faults in the safety option can then be acknowledged by a rising edge via the "Fault acknowledgment" bit in the safe process output data.
A critical fault can only be acknowledged by switching the supply voltage off and on.
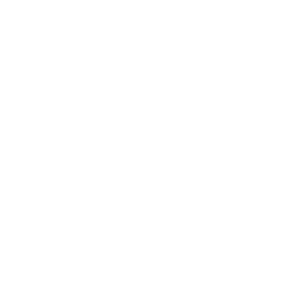
DANGER
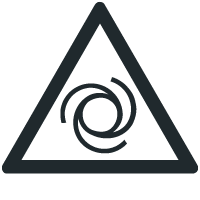
Depending on the connection, MOVISAFE® CS..A can deactivate the STO safety sub-function after the acknowledgment. This can cause an immediate restart of the system.
Severe or fatal injuries.
- Make sure that no person is in the hazardous area of the system during the acknowledgment.
- Make sure that the STO safety sub-function is active via F-DI or safe communication during the acknowledgment.
Existing limit violations of the safety sub-functions are deleted by parameterizing, creating the acceptance report, and publishing the acceptance. Start inhibit is set to prevent the system from switching to operation afterwards.
For details on the cause of the STO, refer to MOVISUITE® in the menu "Diagnostics” > "MOVISAFE® CS.." in the menu item "STO status" in the parameters Cause for start inhibit (8700.124) and Cause for STO (8700.85).