Torque < 0
The following application example shows how to control the "Torque control" operating mode in the IEC program.
Control
Control the axis in the Torque structure as follows:
- To activate the operating mode, set xActivate to "TRUE".
- Define the setpoints for lrVelocityMax, lrVelocityMin, and lrTorque.
- To start the operating mode, set xStart to "TRUE".
Interface in the IEC Editor
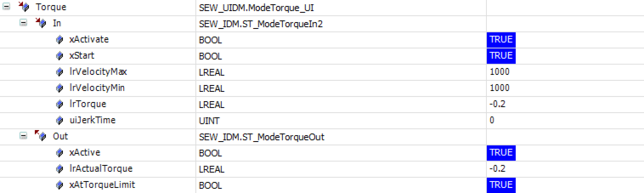
Note:
When the setpoint torque is reached, you will receive the feedback xAtTorqueLimit = "TRUE" in the OUT structure.
Trace recording
The following trace recording shows the profile of current speed and current torque when starting the operating mode with the values set as described above. The current torque is set immediately to the required torque when starting. The xAtTorqueLimit feedback is "TRUE". The axis accelerates with the torque in negative direction. When the maximum speed is reached, the current torque is reduced and the xAtTorqueLimit status variable is set to "FALSE".
[1] | Torque.In.xActivate |
[2] | Torque.In.xStart |
[3] | Torque.In.lrVelocityMax |
[4] | Torque.In.lrTorque |
[5] | Torque.In.xAtTorqueLimit |
In the following trace recording, the axis is initially held at standstill by the load. The current speed is zero and the xAtTorqueLimit status variable is set to "TRUE". Then the load suddenly disappears and the axis accelerates in negative direction. The current torque is reduced as soon as the maximum speed is reached. The xAtTorqueLimit status variable is accordingly set to "FALSE".
[1] | Torque.In.xActivate |
[2] | Torque.In.xStart |
[3] | Torque.In.lrVelocityMax |
[4] | Torque.In.lrTorque |
[5] | Torque.In.xAtTorqueLimit |
Note:
The scenario under consideration here occurs, for example, in the case of material tearing in a winder operated in torque control mode. It is important that the axis speed does not exceed the lrVelocityMin limit.